步入式試驗箱作為環(huán)境模擬設備,其制冷系統(tǒng)在寬溫域運行中面臨能效與控溫精度的雙重挑戰(zhàn)。在 -70℃至 150℃的運行范圍內(nèi),傳統(tǒng)制冷系統(tǒng)存在低溫段能效比低、負荷波動適應性差等問題,能效優(yōu)化需突破多溫區(qū)動態(tài)匹配、熱損失抑制與智能調(diào)控的技術(shù)瓶頸。 動態(tài)負荷匹配技術(shù)是能效提升的核心。采用雙壓縮機復疊式制冷架構(gòu),低溫段啟用渦旋式壓縮機(能效比 2.8-3.2),高溫段切換至變頻活塞壓縮機,通過負荷預測算法實現(xiàn)壓縮機容量 20%-100% 無級調(diào)節(jié)。創(chuàng)新設計分液均勻的多支路蒸發(fā)器,配合電子膨脹閥的脈沖寬度調(diào)制(PWM)控制,使制冷劑流量調(diào)節(jié)精度達 ±2%,部分負荷能效提升 30%。
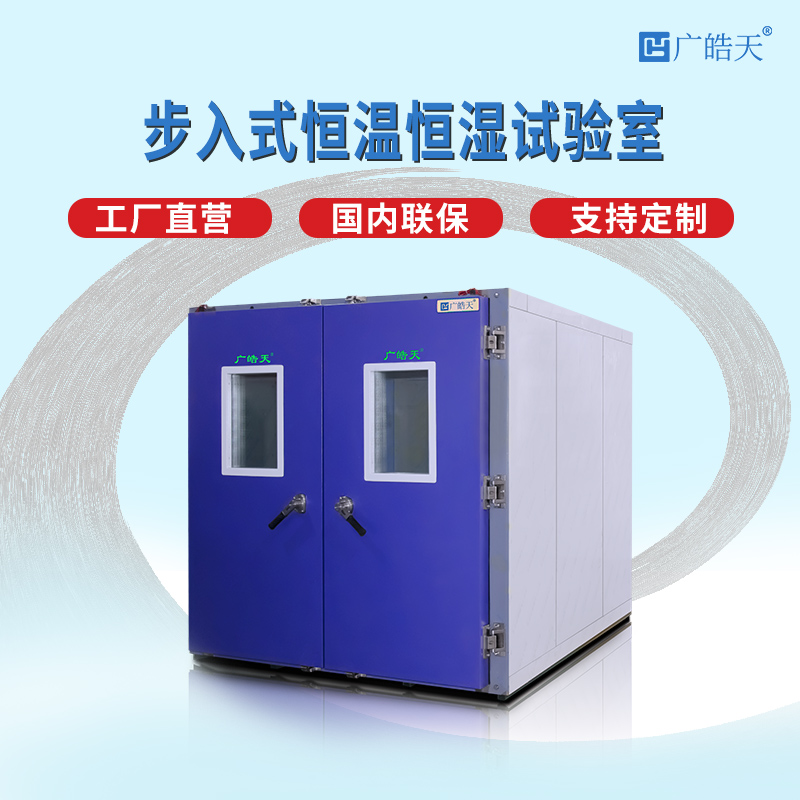

熱管理系統(tǒng)優(yōu)化降低能量損耗。采用納米氣凝膠復合保溫材料(導熱系數(shù)≤0.018W/(m?K))構(gòu)建三層保溫結(jié)構(gòu),結(jié)合紅外加熱膜的分區(qū)控溫設計,使箱體熱損失降低 25%。開發(fā)熱回收回路,將冷凝熱通過板式換熱器回收至預熱系統(tǒng),冬季工況下輔助加熱能耗減少 40%。針對開門操作的冷量流失,配置風幕隔離系統(tǒng)與快速補冷策略,溫度恢復能耗降低 15%。
智能控制策略實現(xiàn)能效精準調(diào)控。建立制冷系統(tǒng)能效模型,通過自適應 PID 算法動態(tài)平衡制冷量與熱負荷,在 ±0.5℃控溫精度下,壓縮機啟停周期延長至 45 分鐘以上。引入深度學習預測控制,基于歷史運行數(shù)據(jù)訓練負荷預測模型(預測誤差≤5%),提前 15 分鐘調(diào)整運行參數(shù)。開發(fā)能效 - 精度動態(tài)權(quán)重控制邏輯,在非嚴苛測試階段自動切換節(jié)能模式,綜合能效提升 22%。
性能驗證體系確保技術(shù)實效。通過焓差法測試,系統(tǒng)在 -50℃工況能效比提升至 1.8 以上,較傳統(tǒng)方案提高 25%。連續(xù)運行測試顯示,采用優(yōu)化技術(shù)后設備日均耗電量降低 18.5kWh。工況驗證表明,在 10℃/min 快速降溫過程中,制冷系統(tǒng) COP 穩(wěn)定性提升 30%,為高精度環(huán)境模擬設備的節(jié)能升級提供了系統(tǒng)性技術(shù)方案。