雙相不銹鋼鋼管對接環(huán)焊縫的相控陣超聲檢測
近年來,微電子和計算機技術(shù)飛速發(fā)展,促成了集相控陣信號產(chǎn)生、數(shù)據(jù)處理、顯示和分析等功能于一體的相控陣儀器的發(fā)展。隨著國內(nèi)外(美國ASME、國際標(biāo)準(zhǔn)ISO以及中國GB和NB)相控陣超聲檢測標(biāo)準(zhǔn)的完善,相控陣超聲檢測已廣泛應(yīng)用于海工、船舶、航空航天、石油化工、火電、核電等行業(yè)。
在設(shè)計時,對于海上油氣工廠(FPSO)上建模塊中材料為A790-S31803,規(guī)格為直徑610mm,壁厚46mm的管線環(huán)焊縫,需要進(jìn)行射線檢測。由于射線具有電離輻射,對檢測人員的人身安全危害嚴(yán)重,故在管線合攏組裝的過程中,不能實現(xiàn)射線檢測中心曝光,從而降低了射線檢測效率,影響項目進(jìn)度。因此,承建方、檢測公司、業(yè)主和監(jiān)造方進(jìn)行協(xié)商后,建議采用相控陣超聲檢測代替射線檢測進(jìn)行現(xiàn)場檢測。在實施相控陣超聲檢測前,需要使用帶缺陷的模擬試塊進(jìn)行校準(zhǔn),以確定檢測結(jié)果的可靠性。
試樣的制作
試樣包括靈敏度對比試塊和用于驗證的人工缺陷模擬試管。
靈敏度對比試塊的制作
按照標(biāo)準(zhǔn)ASME BPVC.V-2019《鍋爐及壓力容器規(guī)范 第V卷 無損檢測》第4章焊縫超聲波檢驗方法中校準(zhǔn)試塊的要求,加工了兩種靈敏度對比試塊。
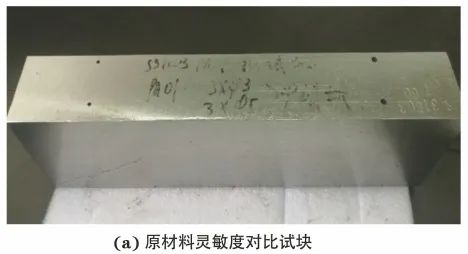
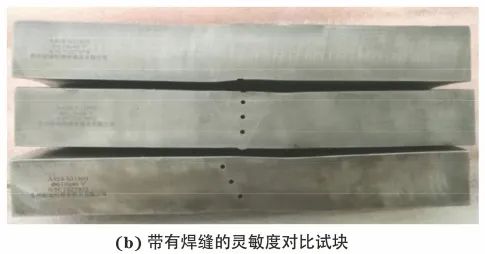
圖1 靈敏度對比試塊實物
如圖1(a)所示,在原材料上加工長橫孔反射體,制作原材料靈敏度對比試塊,用于楔塊延遲的校準(zhǔn)。
如圖1(b)所示,按照焊接工藝焊接后進(jìn)行切割,制作帶有焊縫的長橫孔和刻槽的靈敏度對比試塊,用于靈敏度校準(zhǔn)和TCG(時間校正增益)曲線的制作等。
反射體(長橫孔和刻槽)的詳細(xì)參數(shù)如下:
原材料對比試塊
試塊編號:PAUT-SS-01
人工反射體類型:長橫孔
長橫孔位置:T/4、T/2、3T/4(T為試件厚度)
長橫孔尺寸:ф3mm×80mm
帶焊縫對比試塊
試塊編號:T027973
人工反射體類型:長橫孔
長橫孔位置:焊縫中心:T/4、T/2、3T/4
長橫孔尺寸:ф3mm×70mm
試塊編號:T027972
人工反射體類型:長橫孔
長橫孔位置:坡口熔合線:T/4、T/2、3T/4
長橫孔尺寸:ф3mm×70mm
人工反射體類型:刻槽
刻槽位置:焊縫上表面
刻槽尺寸:70mm×1mm×2mm
試塊編號:T027974
人工反射體類型:刻槽
刻槽位置:焊縫下表面
刻槽尺寸:70mm×1mm×2mm
模擬試管的制作
人工缺陷模擬試管采用切除對比試塊后的余料制作,依據(jù)ASME BPVC.V-2019第4章強制性附錄IX中對于缺陷定量和分類的規(guī)程評定要求,確定缺陷的數(shù)量和位置。
為了確定單面單側(cè)掃查工藝的可行性,在人工缺陷模擬試管上共制作了兩組人工缺陷共6個,分別為上表面缺陷2個、內(nèi)部缺陷3個以及根部缺陷1個,人工缺陷模擬試管實物如圖2所示。

圖2 人工缺陷模擬試管實物
依據(jù)ASME BPVC.V-2019第4章中強制性附錄IX的要求,計算每個缺陷的長度及高度(表面及近表面缺陷按照長高比系數(shù)為0.25計算,焊縫內(nèi)部缺陷按照長高比系數(shù)為0.5計算),人工缺陷模擬試管的結(jié)構(gòu)示意和詳細(xì)參數(shù)如下:
圖3 人工模擬缺陷試管結(jié)構(gòu)示意和缺陷參數(shù)(mm)

1
上表面刻槽
長度10,高度2
(垂直上表面)
2
上表面刻槽
長度10,高度2
(平行融合線)
3
焊縫上部未熔合
長度14,高度5,深10
4
焊縫中心夾渣
長度14,高度5,深20
5
焊縫下部未熔合
長度14,高度5,深30
6
根部刻槽
長度10,高度2,深44
人工缺陷模擬試管
上表面和根部缺陷的檢測
探頭
采用奧林巴斯A26線性和A17、A27矩陣相控陣探頭進(jìn)行檢測,探頭具體參數(shù)如下:
型號:2.25DM7X4-A17
頻率:2.25MHz
晶片數(shù)量:雙晶28(7×4矩陣)
晶片間距:2.71mm
激活孔徑:19mm×12mm
晶片高度:3mm
尺寸:長34mm,寬16mm,高25mm
型號:4DL32-32X12-A26
頻率:4MHz
晶片數(shù)量:雙晶32(線性)
晶片間距:1mm
激活孔徑:32mm×12mm
晶片高度:12mm
尺寸:長48.2mm,寬16.5mm,高26.4mm
型號:4DM16X2-A27
頻率:4MHz
晶片數(shù)量:雙晶32(16×2矩陣)
晶片間距:1mm
激活孔徑:16mm×6mm
晶片高度:3mm
尺寸:長29mm,寬10mm,高20mm
上表面缺陷的檢測
對于上表面刻槽,主要是利用爬波檢測,設(shè)置檢測角度為78°~83°。爬波是縱波從第一種介質(zhì)中以第一臨界角附近(±30′以內(nèi))的角度進(jìn)入第二種介質(zhì)時,在第二種介質(zhì)中產(chǎn)生的沿介質(zhì)表面下一定距離,在橫波和表面縱波之間傳播的峰值波。上表面缺陷檢測時,將不同類型的探頭與楔塊進(jìn)行組合,以觀察檢測效果,其檢測現(xiàn)場示例如圖4所示。
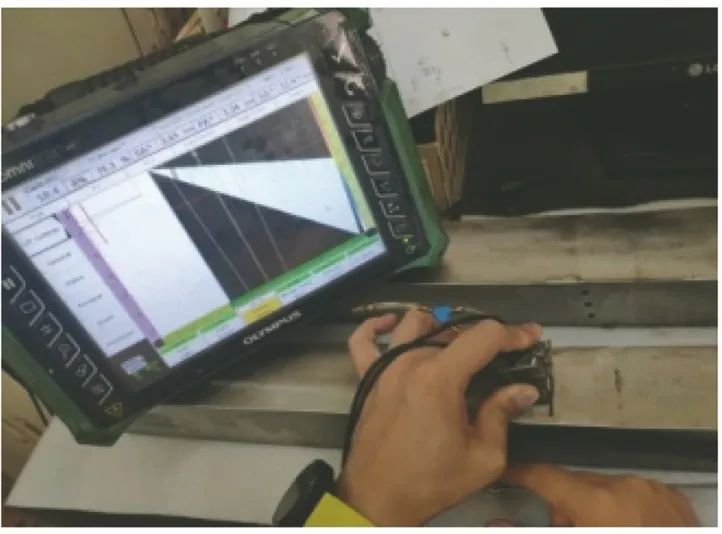
圖4 上表面缺陷的檢測現(xiàn)場示例
將探頭與楔塊組合后,將探頭對準(zhǔn)上表面刻槽,前后移動探頭,使最高波幅達(dá)到滿屏幕的80%,并記錄此時探頭前沿至上表面刻槽的距離。然后后移探頭,波幅緩慢降低,當(dāng)最高波幅降至滿屏幕的20%時,記錄此時探頭前沿至上表面刻槽的距離,檢測結(jié)果如下:
探頭類型 | 楔塊類型 | 探頭前沿至上表面刻槽距離 | |
母材上掃查 | 焊縫上掃查 | ||
A17 | DN55L0 | 17 | 11 |
A26 | DN55L-FD40-SS | 18 | 10 |
A27 | DNCR | 25 | 19 |
由上可知,A27+DNCR探頭與楔塊組合所產(chǎn)生波束移動距離最遠(yuǎn),A17+DN55L0組合效果次之,A26+DN55L-FD40-SS組合效果最差。
根部缺陷的檢測
對于根部缺陷,主要利用一次縱波檢測,設(shè)置檢測角度為37°~50°,使根部刻槽信號達(dá)到滿屏的80%。儀器和探頭組合后顯示的基準(zhǔn)靈敏度:A26探頭的基準(zhǔn)靈敏度為36dB;A27探頭的基準(zhǔn)靈敏度為61dB;A17探頭的基準(zhǔn)靈敏度為51.5dB。
在基準(zhǔn)靈敏度下,A26探頭的噪聲信號幅度為5%,A27探頭的噪聲信號幅度約為7%,而A17探頭的噪聲信號幅度約為15%,根部缺陷的檢測結(jié)果如圖5所示。



圖5 根部缺陷的檢測結(jié)果
A26探頭為線性探頭,且晶片尺寸比其他兩種探頭的大,發(fā)射能量大,因此對同一位置的反射體進(jìn)行檢測時,基準(zhǔn)靈敏度低。
A17探頭雖然基準(zhǔn)靈敏度低,但是檢測頻率為2.25MHz,導(dǎo)致根部刻槽和根部余高信號融合在一起,成為一個脈沖寬度很寬的脈沖信號,且噪聲信號幅度最高。
檢測結(jié)果表明,根部刻槽的檢測效果A26探頭*,A27探頭次之,A17探頭最差。
從以上檢測結(jié)果可以看出,對人工缺陷試管的上表面缺陷應(yīng)采用A27+DNCR組合進(jìn)行檢測,而對焊縫根部,應(yīng)采用A26+DN55L-FD40-SS組合進(jìn)行檢測。
相控陣超聲檢測方案
對材料為A790-S31803的管線環(huán)焊縫進(jìn)行相控陣檢測時,可采用分區(qū)設(shè)置,分區(qū)檢測具有以下優(yōu)勢:
(1) 針對不同檢測位置,設(shè)置不同的聚焦法則,以獲得良好的檢測能力,針對上、下表面的檢測采用深度聚焦,而對焊縫內(nèi)部檢測采用聲程聚焦。
(2) 在實際檢測過程中,偏轉(zhuǎn)角度越大,較深反射體的調(diào)節(jié)越困難。分區(qū)檢測時應(yīng)對較深部位采用較小角度進(jìn)行檢測,以避免大偏轉(zhuǎn)角度調(diào)節(jié)較深反射體的難度。
對于不同分區(qū)的設(shè)置,TCG校準(zhǔn)不同位置人工反射體信號及反射體測量位置如圖6所示。





圖6 不同位置人工反射體信號及反射體測量位置
檢測結(jié)果
為了驗證檢測效果,對圖3所示的人工缺陷試管,分別采用常規(guī)超聲縱波斜入射檢測、射線檢測、相控陣超聲檢測3種方法實施檢測。在相控陣超聲檢測時,實施兩種檢測方案,一種是在焊縫兩側(cè)掃查,模擬單面雙側(cè)檢測;另一種是為了驗證單面單側(cè)檢測效果,實施單側(cè)直管側(cè)掃查+焊縫中心兩個方向的掃查。
上表面刻槽檢測結(jié)果
1號人工缺陷為垂直于工件的上表面刻槽;2號人工缺陷為平行于坡口面的上表面刻槽,傾斜角度為15°±2°,兩種人工缺陷模擬的都是焊縫上表面裂紋,其檢測結(jié)果如下:
(1) 常規(guī)超聲縱波斜探頭檢測,沒有發(fā)現(xiàn)任何信號。
(2) 射線檢測可以清晰發(fā)現(xiàn)缺陷,其結(jié)果如圖7所示。

圖7 1號和2號缺陷的射線檢測結(jié)果
(3) 相控陣超聲技術(shù)檢測,在焊縫兩側(cè)掃查時,由于焊縫蓋帽寬度為38~40mm,A27+DNCR相控陣超聲設(shè)備組合對上表面深度的檢測能力約為19mm,因此只能發(fā)現(xiàn)探頭側(cè)缺陷,不能發(fā)現(xiàn)探頭對側(cè)焊縫的上表面刻槽缺陷,1號缺陷顯示波幅約為95%,而2號缺陷顯示波幅約為60%,2號缺陷上表面刻槽波幅降低主要是因為該刻槽是平行坡口面,焊縫兩側(cè)掃查結(jié)果如圖8所示。


圖8 焊縫兩側(cè)掃查結(jié)果(上表面刻槽)
把焊縫蓋帽磨平后,在焊縫中心采用A27+DNCR設(shè)備組合掃查時,可以發(fā)現(xiàn)焊縫邊緣刻槽信號,1號刻槽波幅高度約為40%,2號刻槽波幅高度約為25%,其結(jié)果如圖9所示。因此在焊縫中心檢測時,需要仔細(xì)辨別超過20%波幅的上表面信號,必要時需要輔助表面檢測方法加以驗證。


圖9 焊縫中心掃查結(jié)果(上表面刻槽)
坡口未熔合檢測結(jié)果
3號和5號人工缺陷分別位于焊縫兩側(cè)坡口熔合線處,且為上、下兩個不同區(qū)域,檢測結(jié)果如下:
(1) 采用常規(guī)超聲縱波斜探頭檢測,在焊縫蓋帽沒有磨平時,臨近上表面的3號缺陷無法檢出;用45°縱波和60°縱波斜探頭均可在焊縫兩側(cè)檢出位于焊縫中下部位的5號缺陷,45°縱波斜探頭檢測的最高波幅為SL+0.5dB,60°縱波斜探頭檢測的最高波幅為SL+6.3dB。將焊縫余高磨平后,使用縱波45°斜探頭騎在焊縫上掃查時,可以在其對側(cè)發(fā)現(xiàn)3號缺陷,波幅為SL+3.2dB,檢測結(jié)果如圖10所示。



圖10 3號和5號缺陷常規(guī)超聲檢測結(jié)果
(2) 采用射線檢測可以發(fā)現(xiàn)兩個缺陷,其結(jié)果如圖11所示。

圖11 3號和5號缺陷射線檢測結(jié)果
(3) 相控陣超聲采用A27+DNCR設(shè)備組合進(jìn)行檢測,3號人工缺陷位于坡口熔合線靠近上表面的位置,因此探頭位于缺陷對側(cè)檢測時波幅高,而在缺陷側(cè)檢測時波幅低,這是由于相控陣大角度偏轉(zhuǎn)角在缺陷對側(cè)檢測時,缺陷與大角度波束接近垂直,而在缺陷側(cè)檢測時,波束入射與缺陷有較大的傾角,因此3號人工缺陷對側(cè)波幅為156%,而缺陷側(cè)波幅為40%;5號人工缺陷位于坡口熔合線靠近焊縫根部的位置,在焊縫兩側(cè)掃查均可得到滿意的檢測結(jié)果,缺陷側(cè)波幅高度為88%,對側(cè)波幅高度為249%,檢測結(jié)果如圖12所示。

圖12 A27+DNCR組合的缺陷檢測結(jié)果
為了驗證單側(cè)檢測結(jié)果,焊縫余高磨平后,在焊縫中心用A27+DNCR設(shè)備組合檢測后發(fā)現(xiàn),3號人工缺陷波幅為250%,5號人工缺陷波幅為94%,此次檢測波幅高度均高于人工缺陷側(cè)的波幅,且檢測信號的位置也處于坡口融合線的位置,更容易對缺陷定性,如圖12所示。
針對焊縫中下部5號人工缺陷的檢測效果,也采用A26+DN55L-FD40-SS組合,使用與A27+DNCR組合相同的聚焦法則在焊縫兩側(cè)檢測,檢測結(jié)果表明,5號人工缺陷對側(cè)波幅為250%,5號人工缺陷側(cè)波幅為94%,波幅均高于A27+DNCR組合的檢測效果。A26+DN55L-FD40-SS設(shè)備組合的檢測結(jié)果如圖13所示。

圖13 A26+DN55L-FD40-SS組合的缺陷檢測結(jié)果
焊縫中夾渣物檢測結(jié)果
4號人工缺陷為內(nèi)部夾渣,位于焊縫中心位置,其檢測結(jié)果如下:
(1) 常規(guī)超聲縱波斜探頭檢測,只有采用60°縱波探頭檢測時能夠發(fā)現(xiàn),在焊縫一側(cè)采用60°縱波進(jìn)行檢測,缺陷波幅高度為SL-10.4dB,而在另一側(cè)無法檢出,檢測結(jié)果如圖14所示。

圖14 4號缺陷常規(guī)超聲波檢測結(jié)果
(2) 4號缺陷射線檢測結(jié)果如圖15所示。

圖15 4號缺陷射線檢測結(jié)果
(3) 相控陣超聲檢測,4號人工缺陷預(yù)埋藏深度約為20mm。A27+DNCR在兩側(cè)均能發(fā)現(xiàn)該缺陷,其最高波幅為41%,另一側(cè)波幅為27%,這是由于缺陷傾角會導(dǎo)致波幅低,如圖16所示。

圖16 4號缺陷的A27+DNCR檢測結(jié)果
而使用A26+DN55L-FD40-SS設(shè)備組合檢測后發(fā)現(xiàn),缺陷最高波幅為30%,結(jié)果如圖17所示。比較兩種規(guī)格探頭的檢測結(jié)果可知,A27+DNCR設(shè)備組合檢測波幅高度略高,因此A26探頭在該區(qū)域的檢測能力低于A27探頭。

圖17 4號缺陷的A26+DN55L-FD40-SS檢測結(jié)果
根部刻槽檢測結(jié)果
6號人工缺陷為根部刻槽,其檢測結(jié)果如下:
(1) 常規(guī)超聲縱波斜探頭檢測,采用縱波45°斜探頭在焊縫兩側(cè)均能發(fā)現(xiàn)該缺陷,表現(xiàn)為一個刻槽和根部融合在一起的脈沖寬度較寬的反射信號,焊縫兩側(cè)的檢測波幅分別為SL-3.2dB和SL+1.8dB,檢測結(jié)果如圖18所示。

圖18 6號缺陷常規(guī)超聲波檢測結(jié)果
(2) 6號缺陷射線檢測結(jié)果如圖19所示。

圖19 6號缺陷射線檢測結(jié)果
(3) 相控陣超聲檢測,A27+DNCR組合在焊縫兩側(cè)均能發(fā)現(xiàn)該缺陷,且有較好的顯示效果,檢測波幅分別為55%和91%,其結(jié)果如圖20所示。
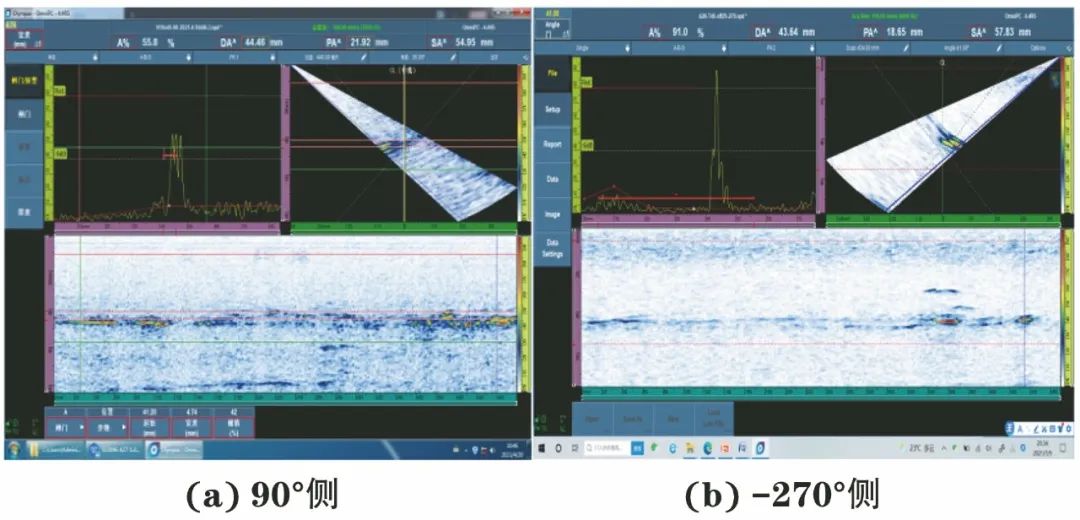
圖20 6號缺陷的A27+DNCR檢測結(jié)果
A26+DN55L-FD40-SS組合也能區(qū)分根部刻槽和余高反射體信號,檢測波幅為61%和185%,其結(jié)果如圖21所示。

圖21 6號缺陷的A26+DN55L-FD40-SS檢測結(jié)果
檢測結(jié)果分析
(1) 綜合比較A27+DNCR組合和A26+DN55L-FD40-SS組合的檢測效果,矩陣探頭A27+DNCR組合主要針對厚度小于30mm部位的檢測,且可在大偏轉(zhuǎn)角時產(chǎn)生爬波以檢測表面缺陷;而線性探頭A26+DN55L-FD40-SS組合主要針對厚度大于30mm部位的檢測,檢測焊縫根部缺陷時有較高的信噪比和分辨力。
(2) 現(xiàn)場對接形式主要為直管與直管對接或直管與部件(法蘭、三通或彎頭)對接。當(dāng)直管與部件對接時,若部件側(cè)滿足探頭掃查空間要求,則可采用直管與直管對接的檢測工藝進(jìn)行單面雙側(cè)檢測,檢測現(xiàn)場如圖22所示。

圖22 直管與構(gòu)件對接檢測現(xiàn)場
(3) 當(dāng)直管與部件對接,部件側(cè)部分位置不滿足掃查空間的要求,檢測現(xiàn)場如圖23所示。此時除了在直管側(cè)掃查外,還應(yīng)把此位置的焊縫余高磨平,在焊縫中心做正反兩次掃查。在對檢測圖譜進(jìn)行分析時,以直管側(cè)掃查為主;對焊縫中心掃查時發(fā)現(xiàn)的可疑位置,需要補充其他方法對表面進(jìn)行檢測,比如增加陣列渦流或其他表面檢測方案;對剩余滿足掃查空間要求的位置,則同樣執(zhí)行單面雙側(cè)檢測。

圖23 直管與部件對接焊縫檢測現(xiàn)場(掃查受限)
結(jié)語
采用相控陣超聲技術(shù)對材料為A790-S31803,規(guī)格為ф610mm×46mm的管線環(huán)焊縫進(jìn)行檢測,檢測結(jié)果表明其具有以下優(yōu)勢:
(1) 相控陣超聲具有良好的缺陷檢測能力,缺陷顯示直觀、重復(fù)性好,且能夠較準(zhǔn)確提供缺陷的長度、深度和高度等信息。
(2) 完成ф610mm×46mm管線對接環(huán)焊縫的檢測用時約30分鐘,射線檢測則需要約792分鐘(以剛出廠Ir192,能量為100Ci,采用雙壁單影透照測算),相比之下,相控陣超聲檢測提高了檢測效率。
(3) 相控陣超聲檢測不產(chǎn)生輻射,不妨礙其他工種的現(xiàn)場施工,提高了生產(chǎn)效率。